Up until now, a wind turbine blade that suffered from loose or damaged bushings either had to be replaced entirely, or the damaged blade needed to be transported to the manufacturer for repair. This resulted in high logistics costs and long downtimes. Today, we can offer a repair solution directly at the wind park site. The blade root is equipped with threaded inserts – also called bushings – that join the rotor blade to the nacelle hub using blade studs.


TURBINE BLADES
BLADE ROOT REPAIRS
Reduce costs and downtime with our blade root repair.
Using precision machining, the damaged bushings at the blade root are repaired at the wind park site, rather than at the blade manufacturer.
This significantly reduces both costs and downtime while offering environmental savings.
These inserts can loosen over time. One cause is shrinkage of the polyester if used as resin. This can lead to microcracks, which endangers the bonding between the bushing and the blade and ultimately endangers the structural safety of the blade root. Bonding failure can lead to the loss of a blade and in worst case to a total turbine collapse. Our efficient blade root repair solution, developed together with We4Ce, an international blade rotor and blade root connection expert, allows the repair to be conducted on-site
TOTAL ECONOMY
Our root blade repair reduced costs as the damaged blade root bushings are repaired on-site with no logistic needed to transport the blade outside the wind park. The exact cost for a blade repair varies from blade to blade and depends mainly on the number of bushings affected and the location of the site. But it is always much cheaper than the standard methods involving off-site repairs or replacing the whole blade.
REDUCED DOWNTIME
With short downtime, the rotor blade can be mounted immediately once repaired, keeping lost production at a minimum.
SUSTAINABILITY
Using precision machining and the patented replacement bushings enable the repair on-site and the need for a potential new blade is avoided. Furthermore, rotor blades are not easily recyclable. Therefore the repair is not only a cheaper option, but it also has a much lower impact on the environment.
LIFETIME EXTENSION
The turbine life time can be extended, an advantage for older units. Finding a replacement blade for older turbines is often difficult and costs are mostly prohibitive. The low repair costs offer an alternative to scrapping the whole turbine and eliminates the reliance on obsolete rotors.
CONTACT US
Our team of experienced professionals will guide and advice you towards the
best possible solution that takes time, economy and durability into consideration.
Søren Kellenberger
Sales Director
+45 25 53 76 50 | ssk@cnconsite.dk

PROCESS
FROM CHALLENGE TO SOLUTION
Quotation request
Planning
Implementation
Handover
Follow-up
Quotation request

The wind park contacts us , reporting damage to the threaded bushings in the blade root.
We discuss with you the extent of the damage. determine if further actions are necessary to get the full picture of the damage
Based on the information, we will issue a quotation for the repair work.
The wind turbine owner approves the proposal and issues a purchasing order.
After that, we can begin the repair within days.
Planning
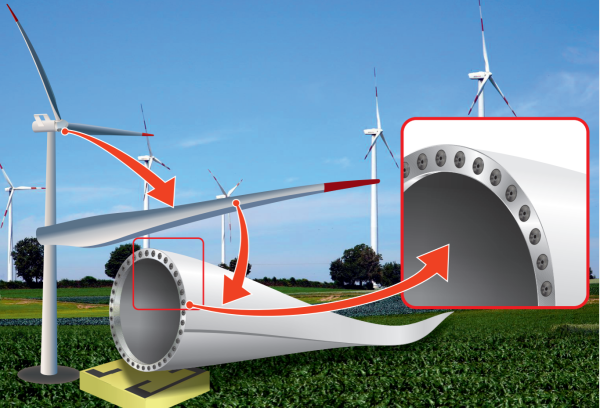
We plan the repairs together with our partner We4Ce.
The job is planned in detail with minimal disruption and downtime in mind.
Implementation

First, the rotor blade is dismounted and placed in a repair environment within the wind park. The repair area can be created on the ground for onshore wind farms or on the deck of a vessel for offshore wind farms.
Once the rotor blade is on the ground and placed in the repair environment, the repair work can start.
The portable pre-programmed CNC machine drills away the faulty bushings, matching the precise dimensions of the specialized replacement bushings, developed and patented by We4Ce.
New inserts are installed and fixed recreating the bond between the insert and the blade,
Upon completion, normally after a few days, the blade can be reinstalled and the turbine can be reinstalled and power production resumed.
Handover

When the repairs of the threaded bushings are complete, our technician discusses the final result with the customer, who approves and signs off.
We issue a repair report to the customer
Follow-up

As part of CNC Onsite’s high quality standards and professional approach, we offer to follow up on the repair job.

SOLUTIONS THAT FIT YOUR NEEDS
„We always take a total economic perspective on our solutions, ensuring that our customers get the most optimal solution in both the short and long term‟
Tobias Jakobsen, Project Engineer
LATEST NEWS
FROM CNC ONSITE

Wind
“Windindustrie in Deutschland” explains how on-site blade root repair works

Wind
4Offshore mentions CNC Onsite and CS WIND Offshore cooperation to mill flanges precisely

Wind
Bearing News explains CNC Onsite/We4Ce’s blade root repair method

Wind
CNC Onsite’s precision machine for flanges explained by Offshore Channel

Wind
Energy Cluster carries CNC Onsite news: Goliath machine for10-meter offshore flanges

Wind
Erhverv+ highlights CNC Onsite’s success on CS WIND Offshore’s transition pieces

Wind
Fastener + Fixing Magazine tells readers effective blade root repair exists

Wind
German Windkraft-Journal mentions CNC Onsite’s mobile precision machine

Wind
Husum Wind press release includes CNC Onsite’s machining of 10-meter flanges

Wind
Metal Supply features CNC Onsite’s precision machining of large offshore flanges

Wind
Metal Supply reports on gantry machine job for Siemens Energy

Wind
Motion & Drives features blade root repair

Wind
North America Clean Energy on the importance of machining offshore flanges to precision

Wind
North American Clean Energy reports on logistics of blade root bushing repairs

Wind
North American Clean Energy with exclusive article by CNC Onsite on flange milling for US offshore wind turbines

Wind
North American Windpower news portal reports on Goliath - the new machine for 10-m diameter offshore flanges

Wind
The German Windmesse mentions precision milling of 10-m-flanges

Wind
The Spanish “El Periodico de la Energía” reports on CNC Onsite’s blade root repairs

Wind
Today’s Machining World has covered solution for machining bolted offshore flanges

Wind
Uptime Tech Podcast shines on yaw ring repair

Wind
Windkraft Journal: CNC Onsite’s Wind Energy Hamburg 2024 highlight offshore flange milling

Wind
Windkraft-Journal mentions CNC Onsite’s milling of offshore flanges

Wind
Windpower Engineering & Development reports: CNC Onsite develops in-turbine method for repairing yaw rings

Wind
WindpowerNL compares blade root inserts to 50 passenger cars pressing onto the blade

Wind
Windtech International features CNC Onsite's yaw ring repair method

Wind
Windtech International reports on progress on CNC Onsite’s flange milling for CS WIND Offshore

Wind
WindTech International: CNC Onsite’s blade root bushing repair with We4Ce

Wind
At Husum Wind 2023: Precision milling of 10-meter wind turbine flanges

Wind
CNC Onsite develops new precision tool for milling 10-meter wind turbine flanges

Wind
CNC Onsite extends up-tower yaw ring repair to more wind turbine platforms

Wind
CNC Onsite first to offer onsite wind turbine blade root repairs

Wind
CNC Onsite to present its yaw ring repair at HUSUM WIND 2023

Wind
CNC Onsite with on-site rotor blade root repair solution at Husum Wind

Wind
CNC Onsite's partner We4Ce for on-site blade root repairs patents retrofit bushings Press release: 28.05.2024

Wind
CS WIND Offshore integrates CNC Onsite’s precision machine for flanges up to 10-meter Press release: 23.9.2024

Wind
New yaw ring repair method makes wind turbine lifetime extension viable

Wind
Paving the way for the future CNC Onsite

Wind
Precision milling of 10-meter wind turbine flanges
